Packaging Automation With Collaborative Robot Solves Labor Shortage
This palletizing automation eliminated the need for a full-time operator, helping address labor shortages and the need to shut down the line when full-time operators were not available.
The packaging automation needed to pick multiple finished plastic injection molded parts and part sizes from a conveyor and palletize them into two 40” x 48” Gaylord containers, adding a slip sheet between each layer of plastic parts. The result of this turnkey packaging automation system solution was one operator needed only once an hour to move the two full Gaylord containers, replace them with two empty containers, and reload the slip sheet tray.
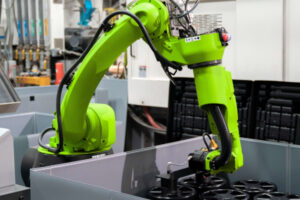
The robust re-deployable turnkey packaging automation solution engineered and manufactured by Robotic Automation Systems employed a FANUC CR15 6-axis collaborative robot on a fully mobile frame so the cell could be moved from one location to another if needed. This FANUC 6-axis collaborative robot was employed because it has more reach while handling higher payloads than other collaborative robots, as well as for its robust design and repeatability.
The packaging automation solution handles five sizes of finished plastic injection molded parts, either one or two parts at a time, and places a 38” x 44” slip sheet between each layer of parts in the Gaylord packaging container. An automatic tool changer is employed for quick product change over between two tool designs, which was able to be implemented because of the higher payload capability of the FANUC CR15 6-axis collaborative robot.
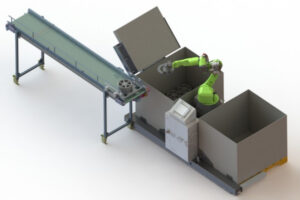
An integrated force sensor within this collaborative robot enables changing payloads on the fly depending on what part was picked and placed at specific locations. This also ensures a safe environment for humans working within proximity to the collaborative robot and packaging automation system, since forces are automatically monitored, stopping the robot if it senses a force higher than programmed and then recovering based on the force sensor feedback.
Robotic Automation Systems programmed our Human-Machine Interface (HMI) with a soft interface between the conveyor pick point since this cell is designed to be mobile. Wireless part detection sensors on the conveyor and a teaching function in the HMI enable a setup fixture to teach the pick location once the conveyor is in place, teaching one master point with all other points offset relative to this master point, so the cell is ready to run quickly when moved to a new location.